KMC Systems and its corporate parent, Elbit America, have responded to the demands of the global pandemic with a host of new safety protocols that have protected workers for months as cases continue to spike across the country.
While just under half of KMC’s 234 employees and consultants have been working from home – relying on Cisco Webex meetings and phone calls to communicate with their colleagues – more than 100 manufacturing, quality and procurement staff continue their essential work producing coronavirus testing instruments on-site at the company’s headquarters in Merrimack, New Hampshire.
Safety protocols put in place
The safety measures put in place to keep the coronavirus from spreading inside the building have altered the way those workers do their jobs, but multiple employees say they have become accustomed to the precautions as the pandemic wears on.
“They’ve become second nature,” said Scott Hastings, a senior technician who works on one of KMC’s production floors. “When we get into the habit of following those protocols, it becomes easier.”
On a weekend in March, a small group of leaders within Elbit America’s Merrimack facility, which houses KMC’s headquarters, met to discuss the COVID-19 safety procedures that would govern the building’s operations. Guidance from the Centers for Disease Control and Prevention, as well as local and state recommendations, informed the strategy.
“What really came out of that was a lot of what we’re still doing today,” said Adam Spencer, a manager of environmental health and safety at Elbit America.
The team established a series of social distancing policies for areas around the building, reducing cafeteria capacity and seating patrons at opposite ends of long tables. Kitchenettes stationed throughout the facility closed as the staff worked to reduce contact with commonly touched surfaces.
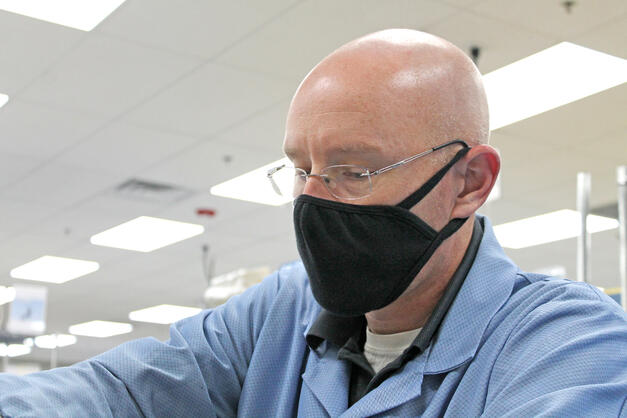
Senior electromechanical assembler Glenn Morley working on the production floor of KMC Systems in Merrimack, New Hampshire.
In April, Elbit America issued a mask mandate that remains in effect. Conference rooms lowered capacity with socially distant zones for each chair taped on the floor. The company also instituted a daily Health Screening questionnaire on May 26 that each employee must fill out at the beginning of every workday ensuring they are asymptomatic.
Since the beginning of the pandemic, only a few employees working in the entire Elbit America Merrimack facility have tested positive. The organization has established a contact tracing program and asks any recent contacts of those who test positive to quarantine for 14 days.
Human Resources Manager Barbara Desmond said the company has tried a number of methods for notifying employees about positive tests.
“We need to balance respect and privacy with being transparent and sharing information,” Desmond said.
In order to share as much information as possible without causing panic, all KMC employees are notified when a positive test occurs, but only those in the affected department are given further details. In accordance with federal privacy regulations, the names of individuals who test positive are always kept in confidence.
As cleaning supplies and other safety equipment became difficult to find in the early days of the pandemic, Elbit America improvised a solution by reaching an agreement with a local hair care product manufacturer to make scented hand sanitizer.
“They needed alcohol, we had alcohol, so we were able to strike a deal where we provided them with isopropyl alcohol and we got hand sanitizer in return,” Spencer said.
After the first 70 gallons of hand sanitizer arrived, a supply of alcohol from Elbit America’s Fort Worth, Texas headquarters allowed the manufacturer to produce a second batch – yielding an additional 100 gallons. As well as supplying all of Elbit America’s locations in the U.S. with hand sanitizer, the deal allowed the company to donate sanitizer to several other organizations, including fire and police departments and nursing homes.
Desmond said maintaining morale among the staff has been challenging with many employees working from home and unable to interact in person. She and her colleagues are devising a number of team-building exercises that can be held virtually to boost spirits, including an interactive game with the company’s executive management.
“It’s a way for our employees to engage with leadership, get to know leadership, have some fun – a fun competition,” Desmond said.
Throughout the pandemic, Elbit America has arranged a number of gifts and giveaways for employees. The organization also participated in Light the Night, an event by the Leukemia and Lymphoma Society to raise awareness and support for cancer treatment. To date, the company has raised over $167,000.
Since the event was held virtually this year, employees took to the streets near their homes and offices one night this fall and took pictures with lights to express solidarity with cancer patients, doctors and researchers.
Despite the challenges associated with following COVID safety protocols, many employees still feel passionately about the work they are doing to help build and distribute instruments that test for the virus.
“My experience with asking employees to get tested really helps me understand the value of getting a quick turnaround on your COVID diagnostic test,” Desmond said. “The sooner you know whether you’re positive or negative, the sooner you can potentially relieve your anxiety and worry about passing it on to your family and friends.
“So, it’s very rewarding to be a part of helping get those systems out there for public use.”
On the production floor, senior technician Scott Hastings was transferred from a different project to help manufacture instruments testing for coronavirus. He said he asked his supervisor to place him there permanently, saying the project “became a very passionate thing” among the staff.
“You really wanted to be a part of it, you really wanted to know that you were doing something,” Hastings said. “It really gives you a sense of that you’re contributing to it. You’re not just looking on the outside and seeing what everybody else is doing.”